By Mark McCulley, Business Owner, Trainer, and Presenter
Over and Over
When weeds grow in a lawn or garden, it’s not enough to cut the top off so you no longer see the weed. The only way to permanently eradicate the weed is by pulling up or destroying the entire root. The same applies in many disciplines. If we do not find the root cause for a problem, then we will meet it again and again.
The world is full of problems which occur over and over:
- Medical: a patient has a perfectly healthy kidney removed instead of the diseased one – an error called “wrong site” surgery
- Manufacturing: a piece of metal is bent backward – the “good side” is facing the wrong way
- Distribution: an order is delivered to the wrong location – the “ship to” address is different than the “bill to” address
Stopping repetitive errors is the goal of Root Cause Analysis, or RCA. This process is used by all industries and all functional areas – nothing is immune to the need for effective root cause analysis.
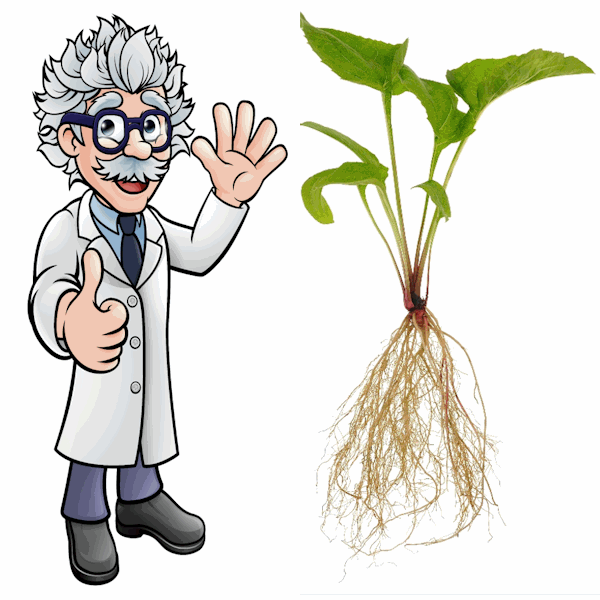
Definitions
Let’s level-set with a few definitions:
- Fault: incorrect directions in the documentation of policies, procedures, or instructions
- Weakness: unclear or missing information which results in more than one possible decision – some of which will result in a non-conformance
- Nonconformance: the non-fulfillment of a requirement in providing a product, service, or fulfilling a policy requirement
- Containment: actions which ensure nonconforming products or services do no harm and do not reach the customer – this treats the effect only
- Correction: replacing a nonconforming product or service – this treats the effect only
- Root Cause: the underlying fault or weakness in a process or system which triggers an undesired event or result – there is often more than one root cause
- Root Cause Analysis: a process, using a set of defined rules and tools, to investigate and categorize nonconformance
- Corrective Action: action taken to address the root cause of a nonconformance and prevent recurrence – an mentioned, there could be multiple actions taken
Five Steps to Success
Root cause analysis can be accomplished in five steps:
- Establish Team
- State the Problem
- Define the Cause
- Test for True Root Cause
- Implement Corrective Action
Let’s look closer at each step.
1. Establish Team
Choosing the most appropriate team members is crucial in finding the root cause.
The person or group responsible for the process in which the nonconformance occurred, or was detected (not always the same), should be the core of the team. However, they should not be tasked with finding the solution on their own. Decision-makers whose work contributes to or is affected by the product or service at hand may also be added.
A solely top-management committee is ineffective. The team must have direct input from front-line workers who are the users of current procedures and will have to implement any changes.
In medical, ethical, and other scenarios, there are times when people involved with the nonconformance are not allowed to be on the team.
Keep the team nimble. Avoid the old management mantra: “A camel is a horse designed by a committee.”
2. State the Problem
A good problem definition, or “problem statement” is best written as a few sentences. It needs to be clear and concise, state the occurrence as it was observed, and describe the immediate effects.
The problem statement should include:
- What happened
- Where it happened
- The date and time it happened
- When it happened (the step in the process)
- How it was observed, measured, or calculated
- What was affected
- Who was involved
- What standard was affected or failed to be met
“A problem well-defined is half-solved”
– John Dewey
Sample Problem Statement
The following is a fictional example from St. Hope Medical Clinic in Athabasca, Manitoba:
“An overdose of Heparin was given to a patient in NICU, at 9:18 AM, shortly before shift change. After the error was discovered, a corrective dose of protamine sulfate was administered by drip. Nurse Osborne and Physician Assistant Smith were the staff on duty. They admitted they failed to cross-check the prescribed Heparin dosage before administering it to the patient.”
Based on this example, would you be able to begin investigating a root cause?
The Titanic Syndrome
“The Titanic sank and 1,500 people died” states two issues, not one. The second may be seen as an effect caused by the sinking, but is the loss of life caused by the actual sinking, or something else? How are the two related? The lives lost issue deserves its own RCA. In your problem statement and in your RCA, you may find there is more than one effect, thus more than one problem, and thus more than one RCA required.
3. Define the Cause
Like any discipline, root cause analysis has rules which can save a lot of time and reduce errors.
Here are a few:
- Clearly show the cause-and-effect relationship – show how a possible cause did, in fact, caused the nonconformance
- Provide evidence showing how the possible cause, if it is repeated, will produce the same effect
- Craft a specific and factual description of what occurred – opinions, statements in the negative, and vague pronouncements don’t provide value
- Identify a system cause, not a human cause – blaming a person does not lead to finding the error within the system
- Pinpoint the preceding step of a violation – late data entry means information was not available for the next operation where the nonconformance occurred
- Failure to act is only causal when there is a duty to act – documentation may not describe what should have been done
Common Tools
In addition to rules, root cause analysis also has many tools which save time and improve results.
A few of the most common:
- Brainstorming: discussing possible causes with others in a cross-functional group helps gain an overview of the problem and aids in a more complete solution
- Fishbone Diagram: also called a “cause and effect” diagram – it was developed by Professor Kaoru Ishikawa to examine problems by looking at categories of “causes” which could have created the “effect” or nonconformance
- 5 Whys: keep asking why as a means to dig deeper into the source of the nonconformance – this is one of the most powerful tools for a root cause investigator
- Scatter Diagram: a visual representation of two variables which can show if there is a correlation – spending more time with your studies will lead to higher grades in your classes
- Control Chart: an enhances run chart which shows upper and lower limits of what is acceptable
- Statistical Analysis: concepts such as mean, mode, range, and standard deviation can describe the amount of variation and other significant information you could not see by just “looking” at the data
- Stratification: grouping data into “subpopulations” which can then be examined discretely – sorting patients by age group to see if this characteristic is correlated with triggering the root cause
- Pareto Analysis: a visual representation which demonstrates the “eighty twenty” rule – 80% of customer complaints come from 20% of your customers
4. Test for True Root Cause
The Root Cause Statement should be simple, consisting of one or two sentences at most.
Typically, leaving out the names of individuals will produce a clearer statement.
One way to test for a true a Root Cause is to think of “the first domino to topple” and show other errors followed as a result.
A functional test traces directly from the proposed root cause, step by step, through actual occurrences, leading directly to the reported nonconformance. If the effects branch off to some other result, then you do not have a true root cause.
In the legal world, the Root Cause is called the “proximate cause” or less formally, the “but-for” cause. According to the old proverb, “for lack of a nail, a shoe was lost; for lack of a shoe, a horse was lost” and so on until “the entire kingdom was lost.” The proximate cause is the one that, ‘but-for’ “the lack of a nail, the incident would not have occurred. If your but-for statement is shown to be true, it indicates a the true root cause.
A final check is to confirm the root cause is actionable. The goal is to stop repetition of nonconformance. Implementation of a solution is mandatory. Therefore, a root cause must be actionable. It cannot be simple “human error” which cannot be prevented. A root cause must describe some flaw in the system.
Questionable Root Causes
Taking short cuts with the rules and tools of defining the cause will lead to questionable conclusions. You can find yourself needing to conduct root cause analysis on your why your root cause analysis does not work!
Common questionable proclamations:
- Employee failed to follow procedure: there is so much more we need to know – is it lack of caring, illness, drug use, laziness, or something else?
- Training is not effective: why is the training viewed as not effective and why was it not discovered sooner?
- Employee assumed: a better word is “guessed” which is a cause – but why are employees making assumptions which result in nonconformances?
- Documentation is out of date: another effect where we do not have the root cause – what is the first domino which topples and leads to out of date documentation?
“If you can’t explain it simply, you don’t understand it well enough”
– Albert Einstein
5. Implement Corrective Actions
Corrective action must directly address the root cause. When tested, it must remedy and prevent recurrence of the original problem.
As stated in the “Definitions” section, corrective action is action taken to address the root cause of a nonconformance and prevent recurrence. This can be one or more steps, and springs from the analysis which produced the Root Cause Statement. It should address a weakness in the system. That may be a weakness in the documentation of a procedure, such as a missing step or poor description.
In ISO 9001:2015, an organization must “evaluate the need for action to eliminate the cause(s)” of the nonconformance. It’s also important to determine if similar problems occur elsewhere. For example, if the root cause is determined to be a weakness in a written procedure, could that same weakness exist in other procedures?
A final step in implementing corrective action is reviewing the effectiveness of the change. This is done by asking if you have truly solved the problem, or merely addressed some effect. An internal audit of the affected process is a common tool in effectiveness review.
Conclusion
Failure to correct the root cause encourages problems to grow, patients or customers to suffer negative outcomes, and lawsuits to be filed!
Water seeks the lowest level. This is true in business as well as nature.
Culture, which is either actively or passively created by top management, is a key element in continuous improvement. In some cultures, people just seek to get through the day expending the minimum amount of effort.
Top management must set the standard to create a culture of excellence, whether in patient care, making burritos, or launching a rocket to Mars.
In many ways, root cause analysis could always lead back to a lack of leadership commitment. Yet, that is a simplistic answer. More questions must be asked. What additional information does top management need to know in order correct cultural weaknesses? How could the culture be changed?
Good questions, and important ones. Perhaps you will be the person who can answer them!
About Mark McCulley
Mark is a business owner, trainer, and presenter with over 40 years of for-profit and non-profit leadership experience. He is an ISO auditor with Professional Quality Assessments in Colorado and is Principal of his own firm, Continual Improvement.
Mark enjoys being physically active, including Nordic skiing, snowshoeing, bicycling, hiking, and vegetable gardening. His two grown children live in California.
Statistics Phobia
Lessons From Sasquatch
Coaching Root Cause Analysis
Make Process Improvement Stick
Root Cause Analysis: Your Mission…
Subscribe to our newsletter
References
5 Whys video
Root Cause Analysis video
Heparin Dosage Errors example
Checklist Manifesto by Atul Gawande
Organizational Improvement Acronyms by Transformance Advisors
Organizational Improvement Definitions by Transformance Advisors